Introduction to hydrogen gas compressors using metal hydrides
Metal hydride technology is a leading innovation in the field of hydrogen storage, essential for harnessing intermittent energy sources such as solar and wind power. It involves using the absorption properties of metal compounds to efficiently store and release hydrogen gas. These properties can also be used to compress hydrogen from a low-pressure source, such as a gas network or an electrolyzer.
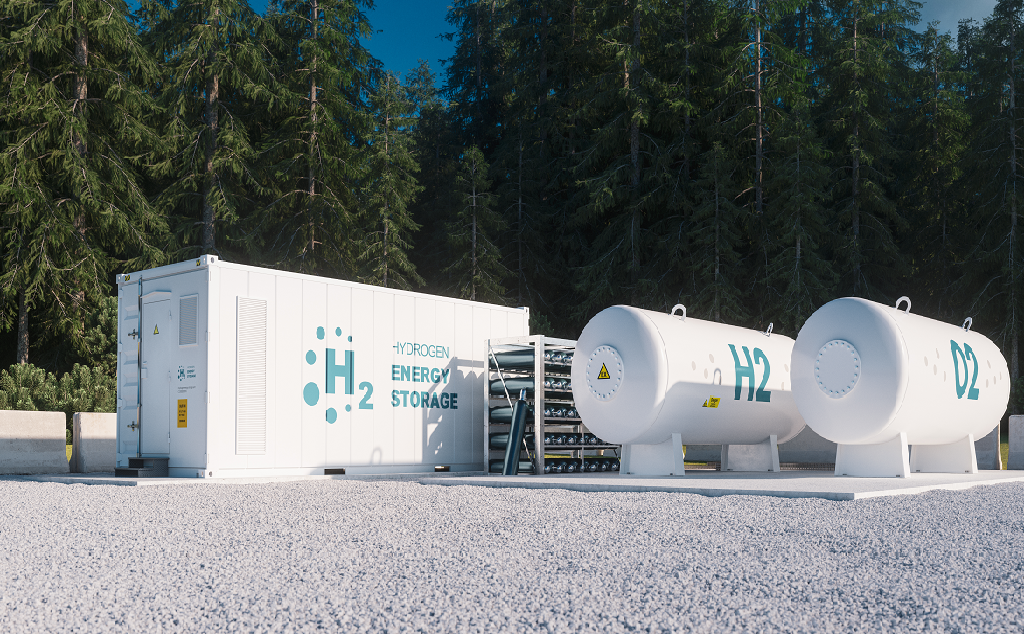
Hydrogen gas compressors using metal hydrides
A metal hydride hydrogen gas compressor consists of four key components:
- A high-pressure reservoir containing a hydride bed. This is connected to a low-pressure hydrogen supply. Several reservoirs can be connected in series to increase the compressor’s charging capacity.
- A pressure sensor measuring the hydrogen pressure in the reservoir.
- A heating element to control the temperature of the reservoir.
- An outlet for releasing the compressed hydrogen to the application or experimental system to be supplied.
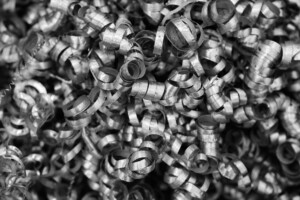
The compression cycle begins with the supply of hydrogen to the tank. During this stage, which takes place at source pressure (around 10 bar) and low temperature, the metal bed is able to absorb a large quantity of gas. The feed valve is then closed, and the reservoir temperature raised. The hydrogen is then released by the metal hydride, inducing a pressure build-up in the reservoir, measured by the pressure sensor. The heating element is controlled to stabilize the reservoir temperature when the set pressure is reached.
The outlet valve can then be opened, and the application supplied with compressed hydrogen. The valve can remain open, and the tank can continue to desorb the hydrogen it contains to maintain the set pressure in the application.
It should be noted that the technique, depending on the nature and properties of the hydride bed used, can also be applied to deuterium compression.
Benefits of hydrogen gas compressors based on metal hydrides
Metal hydride hydrogen compressors meet the challenges faced by laboratories that need to carry out experiments using high-pressure hydrogen. They help improve safety and reduce operating costs.
In fact, compared with conventional mechanical compressors, this equipment uses no moving parts and is therefore much less subject to wear and tear. As a result, they require far less maintenance and present fewer risks of leakage.
Moreover, the hydrogen supply solutions for these metal hydride compressors are all much safer than having a high-pressure hydrogen cylinder inside a laboratory.
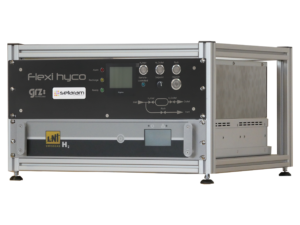
Only the quantity of hydrogen required for the application is compressed and stored in the compressor tank. The volume occupied by the gas is therefore much more limited than that of a conventional gas cylinder and the hydrogen consumption is optimized.
For example, if we take the case of a 200-bar hydrogen cylinder directly connected to an experiment designed to operate at 100 bar via a pressure reducer. When the pressure in the cylinder drops to 100 bar, it becomes useless for the experiment and has to be changed, wasting half the hydrogen in the cylinder. With a compressor running on a 10 bar supply, the hydrogen in the bottle can still be used and compressed, until the pressure in the bottle reaches 10 bar. This means that 95% of the cylinder’s capacity is utilized, instead of 50%.
Finally, the technique, especially when applied to deuterium compression, offers the advantage of being able to recover the gas used by reabsorbing it into the metal bed after the experiment has ended.